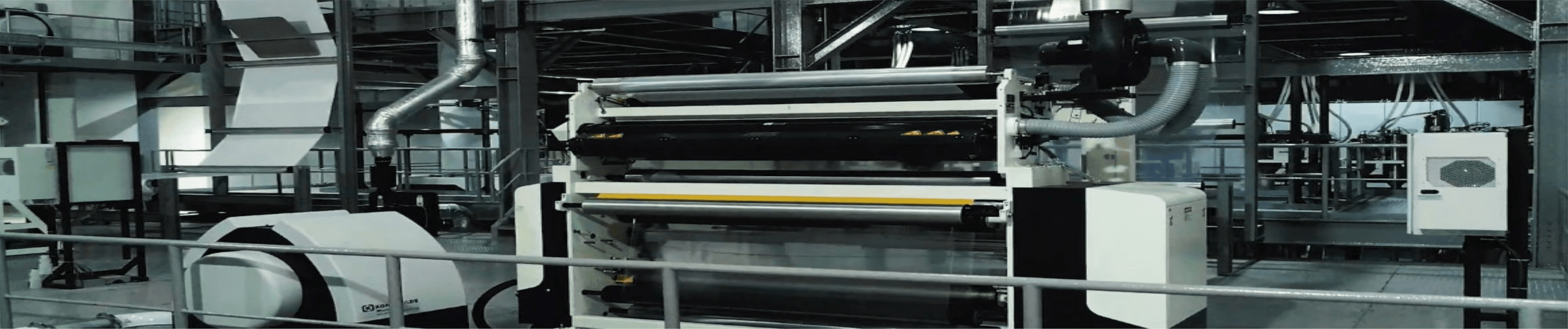
Infrastructure
ROTOGRAVURE
Rotogravure printing is a high-speed, high-quality intaglio process ideal for large-volume production. An 8-color rotogravure setup features eight ink stations that apply various colors to substrates such as BOPP, PET, CPP, Nylon, PVC shrink, PE, PET shrink, and paper, producing detailed and vibrant images. A 9-color rotogravure setup includes an additional ink station, allowing for more complex color variations andspecial effects. Both systems utilize engraved cylinders to transfer ink onto materials, ensuring consistent and precise prints. The extra colour capability in the 9-color process enables more intricate designs, improved colour accuracy, and the application of specialty inks or coatings. This advanced technology meets diverse printing needs, delivering premium quality and intricate designs for large-scale production runs. Our state-of-the-art infrastructure supports 2-color , 6-color , 8-color and 9-color rotogravure printing, ensuring exceptional results for a wide range of materials and applications.
Lamination
Nordmeccanica is renowned for its innovative solventless lamination machines, which are designed for efficient and environmentally friendly lamination processes. These advanced systems utilize adhesive technologies that eliminate the need for solvents, significantly reducing emissions and enhancing workplace safety. Ideal for producing flexible packaging, these machines effectively bond films, foils, and papers without requiring drying ovens, resulting in lower energy consumption and faster production speeds. Nordmeccanica's laminators are praised for their high precision, reliability, and ease of use, featuring automated controls and consistent performance. They support a wide range of substrates, making them versatile solutions for modern packaging needs while maintaining high-quality standards and reducing operational costs. As a leader in the flexible packaging industry, Nordmeccanica sets the benchmark for precision, efficiency, and environmental responsibility with its solventless technology.
Extrusion coating lamination
Our infrastructure boasts a cutting-edge extrusion coating lamination machine, indispensable for applying plastic or polymer layers onto substrates like paper, foil, or fabric. This specialized equipment comprises several key components:
The extruder, featuring a heated barrel and screw to melt and convey polymer resin, alongside a hopper for raw pellet input and temperature control for optimal melting.
-A die assembly, including a flat die and deckling system to regulate film thickness.
-A substrate unwind unit with roll stand and tension control for smooth substrate handling.
-A coating station with coating and nip rollers for precise polymer application and adhesion.
-Optionally, a lamination section with secondary substrate unwind and pressure rollers for composite material production.
-A cooling system with chill rollers and air knives to solidify the polymer.
-A winding unit with rewind rollers and edge trim system for packaging or further processing.
The process involves feeding and melting polymer pellets, extruding them into a thin film, applying the film onto the moving substrate, optionally laminating a secondary substrate, cooling, and rewinding into rolls. Extrusion coating finds extensive use in packaging, textiles, automotive, and construction industries, providing enhanced properties such as moisture resistance, durability, and insulation in a wide range of applications.
Pouching units
With over 50 Pouching units, our capabilities encompass a wide array of flexible packaging pouch types, catering to diverse product requirements. Some of the key types we offer include:
PP covers printed – Inner cover and secondary Packing.
Stand-up Pouches:
Featuring an oval-shaped bottom for stability.
Equipped with a tear-off tab and plastic zip-lock for convenient resealing
Gusseted Pouches:
Stand-up packaging with square or rectangular bases.
Enhanced with indents on the sides, folded-down tops, and resealable tabs.
Pillow Pouches:
Characterized by two flat, sealed panels.
Easy peel opening facilitated by pulling panels in opposite directions
Three-Side-Seal Pouches:
Flat pouches sealed on three sides.
Designed with a tear-away lid for easy access to contents.
Sachets:
Small, flat packets sealed on all four sides.
Perfect for single-serve condiments and similar applications.
Idli Dosa batter packaging-
Guzzeted pouchs,Idli dosa packaging utilizes laminates to balance freshness, moisture prevention, hygiene, and convenience. Layers include printing, moisture barrier, strength, sealing, and optional features like oxygen barrier and peelable layers.
Liquid Pouch Packaging:
Includes spout pouches and clear pouches with various design variations tailored for liquid products.
Our flexible pouch packing machines are equipped to handle these diverse pouch types efficiently, ensuring optimal packaging solutions for a wide range of products. Whether it's stand-up pouches, gusseted pouches, pillow pouches, or sachets, we offer adaptable packaging formats to meet specific needs and preferences, providing convenience and reliability in product packaging.
Bopp folding machine
A BOPP folding machine is a specialized piece of equipment designed to fold Biaxially Oriented Polypropylene (BOPP) film, a popular material used in packaging, printing, and labeling applications. These machines are commonly used in the packaging industry for folding BOPP film into various configurations to create bags, sleeves, or other packaging formats.
Key Components and Functions: Feeding Mechanism:
Accepts rolls of BOPP film and feeds them into the folding machine. Folding Section:
Utilizes folding mechanisms to fold the BOPP film according to the desired configuration. Can incorporate multiple folding stations for complex folding patterns. Cutting Unit:
Optionally includes a cutting mechanism to trim the folded film to the desired length. Control System:
Manages the operation of the machine, including speed control, folding patterns, and safety features.
Process Overview:
Material Loading:
Rolls of BOPP film are loaded onto the machine's feeding mechanism. Folding:
The BOPP film passes through the folding section, where it undergoes the desired folding pattern, such as edge folding, bottom folding, or gusset folding. Cutting (if applicable):
Optionally, the folded film can be cut to the desired length using the cutting unit. Final Product Output:
The folded and/or cut BOPP film is outputted from the machine for further processing or packaging.
Aluminum container manufacturing
An aluminum foil container manufacturing machine is specialized equipment designed to produce aluminum foil containers of various shapes and sizes for packaging purposes. These machines typically consist of multiple components, including a feeder for aluminum foil rolls, a molding system to shape the foil into containers, a cutting mechanism to trim excess material, and a stacking or packaging unit for finished products. The process involves feeding aluminum foil into the machine, where it undergoes molding, cutting, and stacking to produce ready-to-use containers. Aluminum foil containers manufactured by these machines find widespread use in the food industry for packaging items such as take-out meals, bakery products, and ready-to-eat snacks due to their lightweight, recyclability, and heat-sealing properties.
PP blown film
PP blown film machines utilize blown film extrusion to create polypropylene (PP) films. Beginning with resin pellets, the process involves melting, conveying, and shaping the PP into a continuous tube, inflated with compressed air to form a bubble. Cooling and control mechanisms ensure proper solidification, thickness, and diameter. Advanced features like automatic gauge control and bubble stabilizers enhance quality assurance. The resulting PP films find extensive use in packaging, including food packaging, shopping bags, agricultural films, and industrial liners. PP blown film machines are crucial for efficiently producing high-quality films tailored to diverse application needs, thanks to their precision and versatility.
LDPE Extruder
LDPE extruder machines in our arsenal is pivotal in crafting LDPE films, prized for their versatility in packaging. Monolayer machines create single-layer films by melting LDPE pellets, shaping them with precision, cooling, and winding for further processing. Multilayer machines elevate LDPE films by co-extruding multiple layers, each tailored for specific functions like strength or barrier properties. Equipped with cutting-edge features such as automatic gauge control and inline quality monitoring, these machines ensure consistent film quality, meeting stringent packaging demands. LDPE films, produced with utmost precision and quality, find extensive use in various packaging applications, including food, industrial, and agricultural sectors.
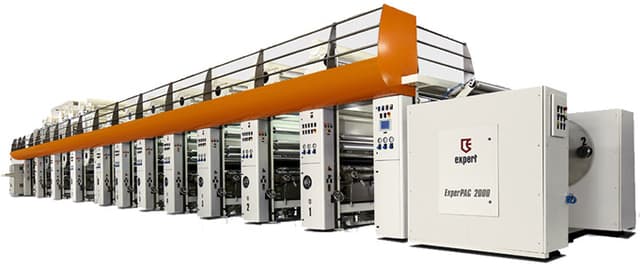
Get connected
Send Email
digital@vaibhavprintpack.in
Contact Us
+91 9606447692
Address
36, 3rd Floor, Vasavi Avenue,
11th Main Rd, 5th Block,
Jayanagar, Bengaluru,
Karnataka 560041